5S trong nhà máy
Lợi ích từ công cụ 5S trong sản xuất
Khái niệm 5S (5S methodology) bắt nguồn từ Nhật Bản vào đầu những năm 1980 thế kỷ XX. Theo định nghĩa công cụ 5S là Seiri (Sàng lọc những thứ không cần thiết tại nơi làm việc và bỏ đi), Seiton (Sắp xếp mọi thứ ngăn nắp để dễ tìm, dễ thấy, dễ lấy), Seiso (Sạch sẽ vệ sinh thiết bị, dụng cụ và nơi làm việc), Seiketsu (Săn sóc nơi làm việc bằng cách luôn thực hiện 3S trên) và Shitsuke (Sẵn sàng giáo dục rèn luyện để mọi người thực hiện 4S trên một cách tự giác).
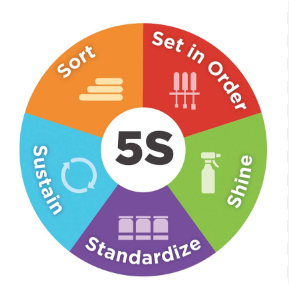
Công cụ 5S là công cụ được nhiều doanh nghiệp lựa chọn áp dụng để đổi mới quản lý hoạt động
Công cụ 5S trong sản xuất là gì?
Chúng ta vẫn thường bắt gặp ở bất cứ nhà máy nào của Nhật Bản đều thấy những tấm biển khá lớn với khẩu hiệu: “Thực hiện tốt 5S”. Tại nơi này, tiêu chuẩn 5S đã trở thành những nguyên tắc và tập quán quản trị trong doanh nghiệp. Tiêu chuẩn 5S được áp dụng lần đầu tiên ở tập đoàn Toyota và phát triển rất nhanh sau đó ở các công ty Nhật Bản.
5S là tên của một phương pháp quản lý, sắp xếp nơi làm việc. Nó được viết tắt của 5 từ trong tiếng Nhật gồm: Seiri (Sàng lọc), Seiton (Sắp xếp), Seiso (Sạch sẽ), Seiketsu (Săn sóc), và Shitsuke (Sẵn sàng).
Sàng lọc (Seiri): Có nghĩa là phân loại, tổ chức các vật dụng theo trật tự. Đây chính là bước đầu tiên doanh nghiệp cần làm trong thực hành 5S. Nội dung chính của S1 là phân loại, di dời những thứ không cần thiết, có thể bán đi hoặc tái sử dụng.
Sắp xếp (Seiton): Sau khi đã loại bỏ các vật dụng không cần thiết thì công việc tiếp theo là tổ chức các vật dụng còn lại một cách hiệu quả theo tiêu chí dễ tìm, dễ thấy, dễ lấy, dễ trả lại.
Sạch sẽ (Seiso): Thường xuyên vệ sinh, giữ gìn nơi làm việc sạch sẽ thông qua việc tổ chức vệ sinh tổng thể và tổ chức vệ sinh hàng ngày máy móc vật dụng và khu làm việc. S3 hướng tới cải thiện môi trường làm việc, giảm thiểu rủi ro, tai nạn đồng thời nâng cao tính chính xác của máy móc thiết bị (do ảnh hưởng của bụi bẩn).
Săn sóc (Seiketsu): Luôn luôn kiểm tra, duy trì 3S ở trên. Bằng việc phát triển S4, các hoạt động 3S sẽ được cải tiến dần dựa theo tiêu chuẩn đã đặt ra và tiến tới hoàn thiện 5S trong doanh nghiệp.
Sẵn sàng (Shitsuke): Là rèn luyện, tạo nên một thói quen, nề nếp, tác phong cho mọi người trong thực hiện 5S.
Lợi ích của công cụ 5S
Nơi làm việc trở nên sạch sẽ và ngăn nắp hơn.
Tăng cường phát huy sáng kiến cải tiến.
Mọi người trở nên có kỷ luật hơn.
Các điều kiện hỗ trợ luôn sẵn sàng cho công việc.
Chỗ làm việc trở nên thuận tiện và an toàn hơn.
Cán bộ công nhân viên tự hào về nơi làm việc sạch sẽ và ngăn nắp của mình.
Đem lại nhiều cơ hội kinh doanh hơn.
Thực hiện tốt 5S sẽ đóng góp cho các yếu tố PQCDSM:
Cải tiến Năng suất (P – Productivity)
Nâng cao Chất lượng (Q – Quality)
Giảm chi phí (C – Cost)
Giao hàng đúng hạn (D – Delivery)
Đảm bảo an toàn (S – Safety)
Nâng cao tinh thần (M – Morale)
Khi thực hiện 5S thành công trong công ty, 5S sẽ đưa lại sự thay đổi kỳ diệu. Những thứ không cần thiết sẽ được loại bỏ khỏi nơi làm việc, những vật dụng cần thiết được xếp ngăn nắp, gọn gàng, đặt ở những vị trí thuận tiện cho người sử dụng, máy móc thiết bị trở nên sạch sẽ, được bảo dưỡng, bảo quản. Từ các hoạt động 5S sẽ nâng cao tinh thần tập thể, khuyến khích sự hoà đồng của mọi người, qua đó người làm việc sẽ có thái độ tích cực hơn, có trách nhiệm và ý thức hơn với công việc.
Mục tiêu chính của công cụ 5S
5S là một phương pháp rất hiệu quả để huy động con người, cải tiến môi trường làm việc và nâng cao năng suất doanh nghiệp.Mục tiêu chính của chương trình 5S bao gồm:
Xây dựng ý thức cải tiến (Kaizen) cho mọi người tại nơi làm việc.
Xây dựng tinh thần đồng đội giữa mọi người.
Phát triển vai trò lãnh đạo của cán bộ lãnh đạo và cán bộ quản lý thông qua các hoạt động thực tế.
Xây dựng cơ sở để đưa vào các kỹ thuật cải tiến.